The real zeal behind railroad maintenance
Written by Mischa Wanek-Libman, editor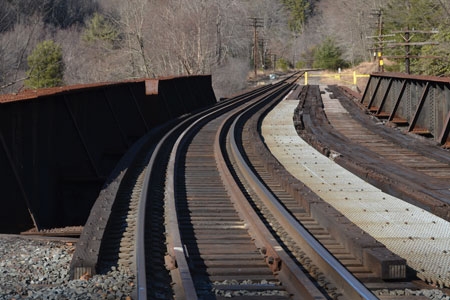
While Reading & Northern may be smaller in size to other railroads, its employees are never short on enthusiasm, dedication and passion when it comes to maintaining its assets.
{besps}April14_shortline{/besps} {besps_c}0|1shortline.jpg|Bridge No. 130.90 deck replacement complete.{/besps_c} {besps_c}0|2shortline.jpg|Bridge No 130.90 deck replacement on R&N’s mainline at MP 130.9, north of Jim Thorpe, Pa.{/besps_c} {besps_c}0|3shortline.jpg|R&N has many high degree curves on its mainline, with some reaching 10 degrees.{/besps_c}
While Reading & Northern may be smaller in size to other railroads, its employees are never short on enthusiasm, dedication and passion when it comes to maintaining its assets.
Success on a small railroad can be attributed to many things, such as good planning, growing traffic volumes and even a little bit of luck. In the case of the Reading & Northern Railroad (R&N), based in Port Clinton, Pa., prosperity comes as a result of all those things, plus a healthy dose of passion and pride in the work being performed.
Chief Executive Officer Andy Muller is an ardent believer in well-maintained track. In 2013, the railroad had what it calls its most productive maintenance year to date. R&N spent $8.7 million of its own capital, no federal or state funds, on its 320 miles, which breaks down to just more than $27,000 per track mile on engineering-related activities.
Erik Yoder, assistant vice president of maintenance of way, wrote in the railroad’s winter edition of its R&N Magazine, “Our track forces are hard at work each and every day. It shows in how clean our railroad looks and the satisfaction we have in a job well done.”
R&N’s 32-man track department had a very busy 2013, beginning with the installation of more than 35,000 crossties on the Lehigh and Reading mainline. Yoder wrote that approximately 13,000 ties were installed between North Reading Yard to just south of Webster; the Pottsville Branch received 2,000 ties and the Lehigh mainline between Independence to just south of Seidel received the remaining 20,000 ties.
The railroad also eliminated 175 joints on its Lehigh and Reading Divisions to prepare for the use of an 88-stone grinding train on those same divisions to re-profile the rail head in order to prolong rail life, ride quality and overall track maintenance.
R&N performed 12 grade-crossing rehabilitations, four of which were complete replacements and eight that needed either the approaches repaved or new timbers installed and, in a few cases, both. Some of the railroad’s bridges also underwent revamping with fresh paint, new no trespassing signs and milepost signs and repairs made to any bridge timber surface defects.
In addition to the work described above, R&N’s Smoothie Gang, a team of tamping and ballast maintenance experts, provided the final polish to many of the railroad’s projects.
“This special gang is our Mark IV and ballast regulator team. They are responsible for applying the finishing touches to any project we complete on the railroad. They are a vital part of every full crossing rehabilitation [and] provide the proper elevation, level and grooming of the railroad,” wrote Yoder. “Every time you see a railroad bed that has no stone on the railroad ties, stone in between each tie or stone gently sloping down away from the ties is all due to the work of the Smoothie Gang. This last step is the moment when we can all look at the railroad and have a great deal of satisfaction.”
With all the work that R&N has taken on in the past year, the big question is where does it get the money? The short answer is the railroad’s owner and CEO Andy Muller, but he explains the Railroad Track Maintenance Tax Credit, better known as 45G, is critical to the R&N maintenance work and its importance can not be overestimated.
“The truth is not really told on the success of the small railroads. There are starting to be more and more successful small railroads. However, in many cases, they are not making a profit in the real world and if they were forced to pay for their own maintenance and they were never allowed to defer maintenance, I don’t know how many would really be profitable out of the 550 [existing small railroads],” said Muller.
“There’s really only two ways to stay in business if you’re a small railroad: One, is getting help from the state and, two, is defer maintenance and, of course, many [smaller railroads] defer maintenance. Here at the Reading and Northern, I love track, but we deferred maintenance for many years because I wasn’t making money. In 2010, we started making a real profit and what really, really pushed us over the top was the 45G credits. There is absolutely no way, even a successful company like mine, could maintain the railroad without these credits,” explained Muller.
Talk in Washington, D.C., does exist that the 45G tax credit could become retroactive if it is passed as part of an extenders package, but Muller isn’t holding his breath, “I don’t make decisions based on the actions of the government. I don’t sit home at night and worry if the 45G tax credit will be passed. I have to do what I have to do. You have to understand, we do nothing with budgets, I just happen to love maintenance-of-way.”
While finding funds isn’t a barrier to the success of the maintenance department, Wesley Westenhoefer, vice president MOW quality control, does point out the obstacles the railroad must contend with.
“Our biggest challenge of late is not having a long enough construction season to accomplish what we would like to accomplish. When you have a CEO whose passion is beautiful track and he has his wallet open, it is hard to keep up,” said Westenhoefer.
Westenhoefer also points to the R&N’s terrain, which poses challenges that many other railroads do not have, such as heavy grades and many eight degree and higher curves.
“It is a constant battle to maintain proper gauge, uniform spirals and correct elevation in many of our curves. In addition, we have six tunnels and 146 bridges to maintain, as well,” said Westenhoefer. “But, we’ve been doing really good, we’ve been keeping up with it.”
He explains that five years ago, Muller implemented a no slow order rule for the railroad. According to Westenhoefer, any slow order must be removed within 24 hours and, if crews are unable to achieve this, they must have written approval from Muller and the railroad’s executive vice president of operations, as well as a very good reason as to why the slow order must remain active.
Too keep up with that kind of high standard, the people you work with is also an important factor of success. R&N handles all maintenance work in house with the exception of major tie projects (1,000-plus ties), rail replacement projects and tunnel work.
“We have a very intense hiring procedure at our company. We receive hundreds of applications a year and are very critical of who we bring in for an interview. Many times, we will interview a potential candidate twice before hiring them,” said Westenhoefer. “We hire smart people who don’t necessarily need to have safety ‘beat’ into them. The safety of our employees is always our top priority and focus. We put a lot of time and energy into our training program for our new employees, as well as recurrent training for our veterans. Our MOW team takes pride in what they do and are always vigilant on going home in the same condition they arrived on a day-to-day basis.”
Staying vigilant in safety and in its dedication to work enabled the railroad to reduce the number of derailments by almost 50 percent from 2012 to 2013.
According to Yoder, maintenance crews are always quick to respond to whatever the need may be from clearing trees from across the tracks following a storm to waking up at 2 a.m. in winter because a temperature drop resulted in a broken rail that need to be repaired immediately to keeping R&N’s switches free of debris or snow, inspecting tracks to catch problems before trains do and many other tasks.
Yoder wrote, “Keeping the trains moving with tireless motivation is what makes this department the best. They are the reason we can again [call 2013] our ‘most productive’ maintenance year on record.”